Faszination Orgelbau
Rieger Orgelbau. Unser Name steht seit 1843 für höchste Qualität im Instrumentenbau. Heute zählen wir zu den größten Orgelbaufirmen weltweit. In unserer Werkstatt in Schwarzach, in Vorarlberg, bauen wir neue Orgeln für Kirchen, Kathedralen, Konzertsäle oder Hochschulen, sowie Kleinorgeln. Darüber hinaus restaurieren wir historische Instrumente.
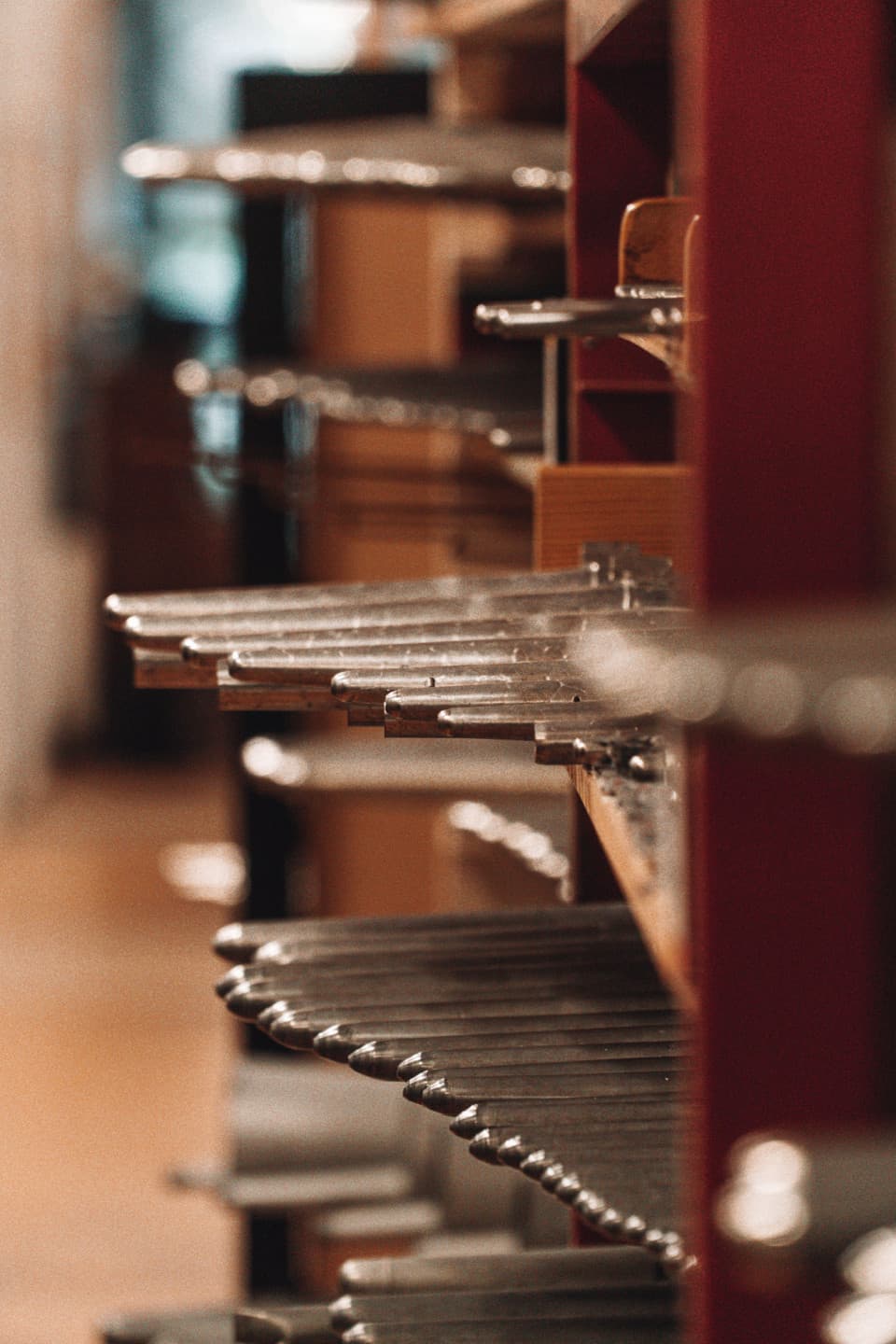
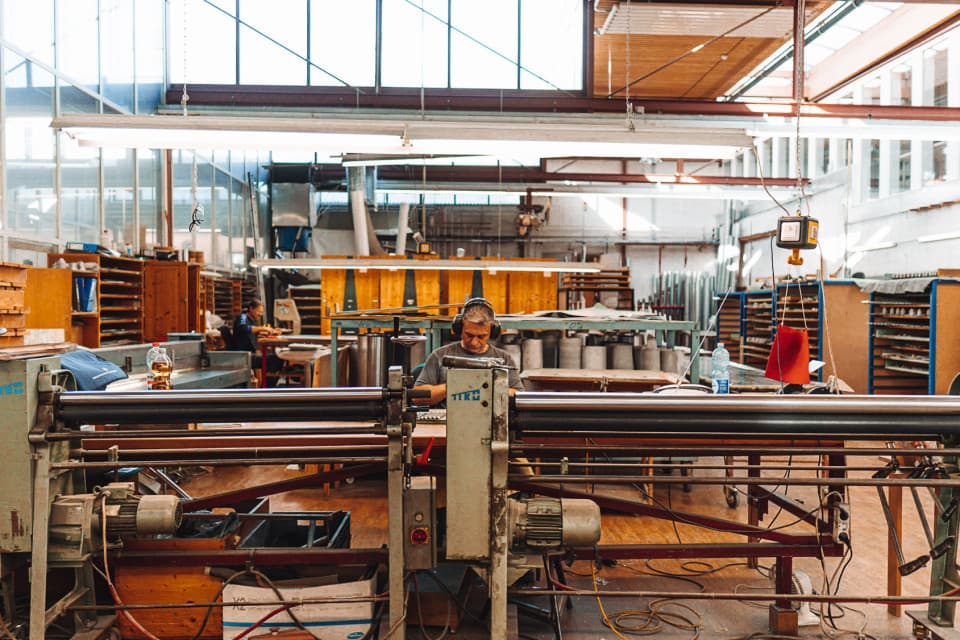
Maximale Perfektion durch handwerkliche Kunst – das macht Rieger aus
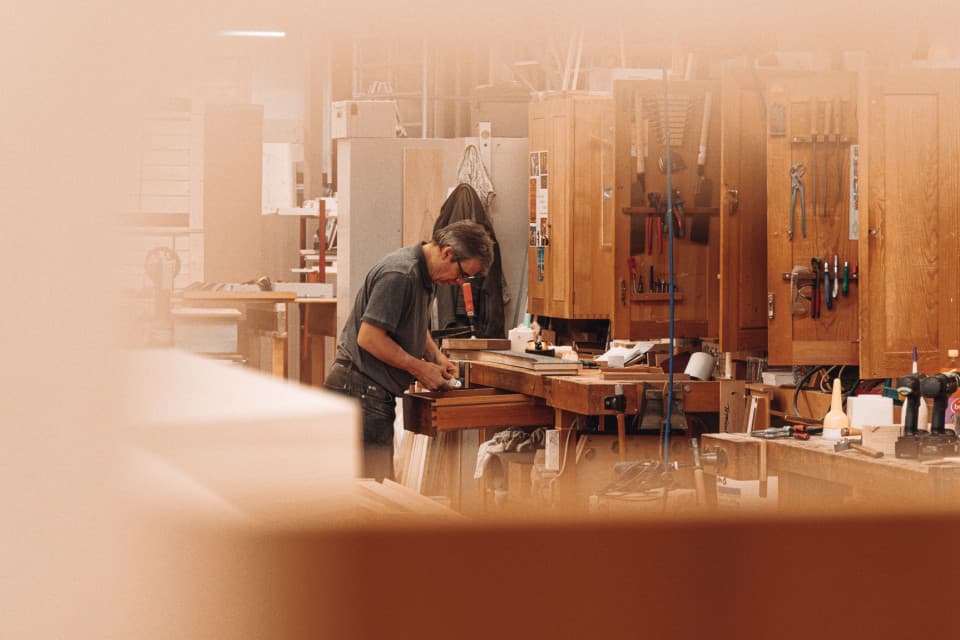
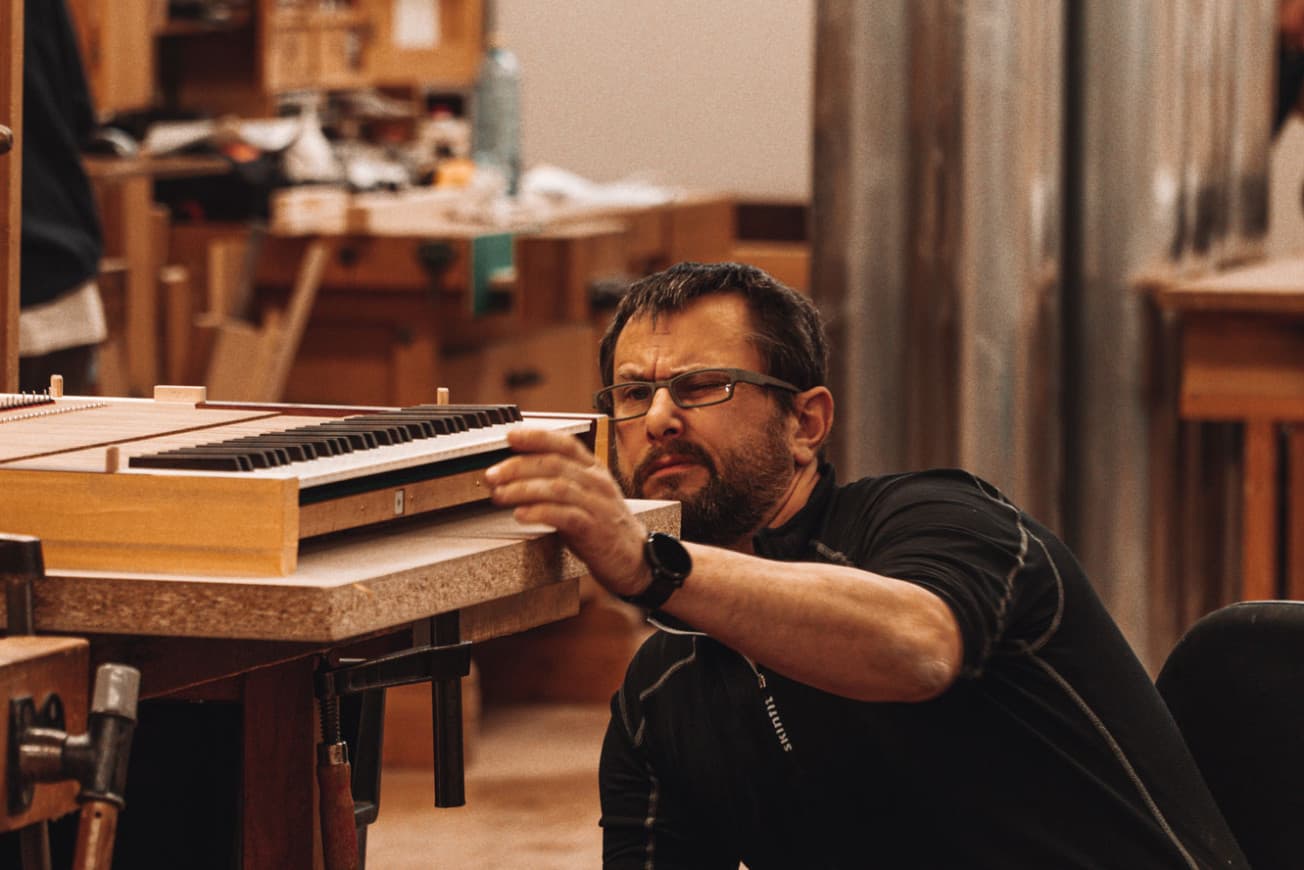
Die Orgel im Wiener Stephansdom mit ihren 134 Registern ist natürlich eines unserer Leuchtturmprojekte.
Neubauten
Raum und Funktion sind maßgebend für eine neue Rieger Orgel. Und umgekehrt. In einem wechselseitigen Prozess entsteht in unserer Werkstatt nach individuellen musikalischen und technischen Aspekten ein einzigartiges und ganzheitliches Instrument.
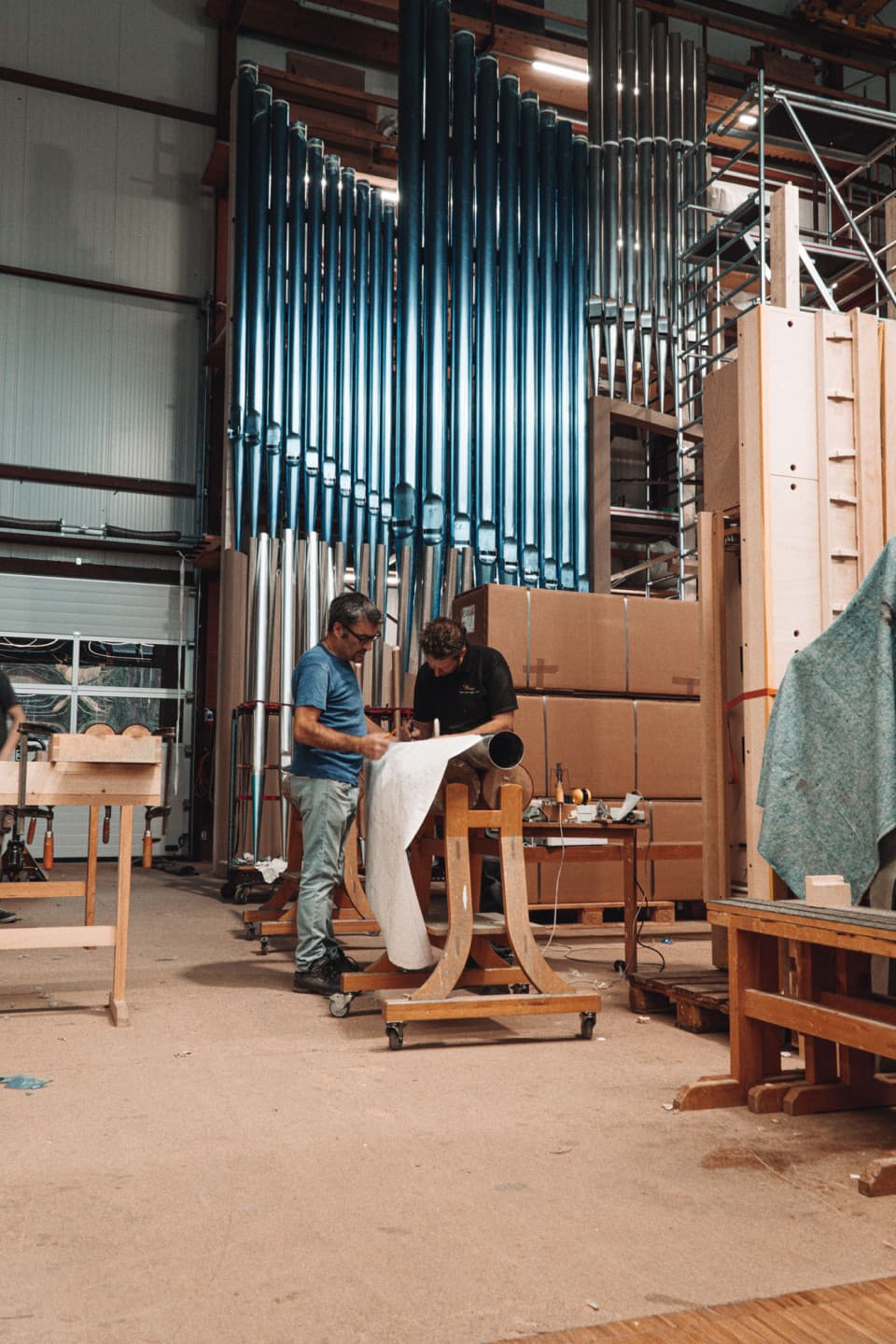
Restaurierungen
Die Restaurierung historischer Orgeln nimmt einen großen Aufgabenbereich bei Rieger Orgelbau ein. Unser Restaurator:innen-Team ist darauf spezialisiert, Instrumente aus verschiedenen Epochen zu reparieren, instand zu setzen und nach Vorbild rekonstruieren.
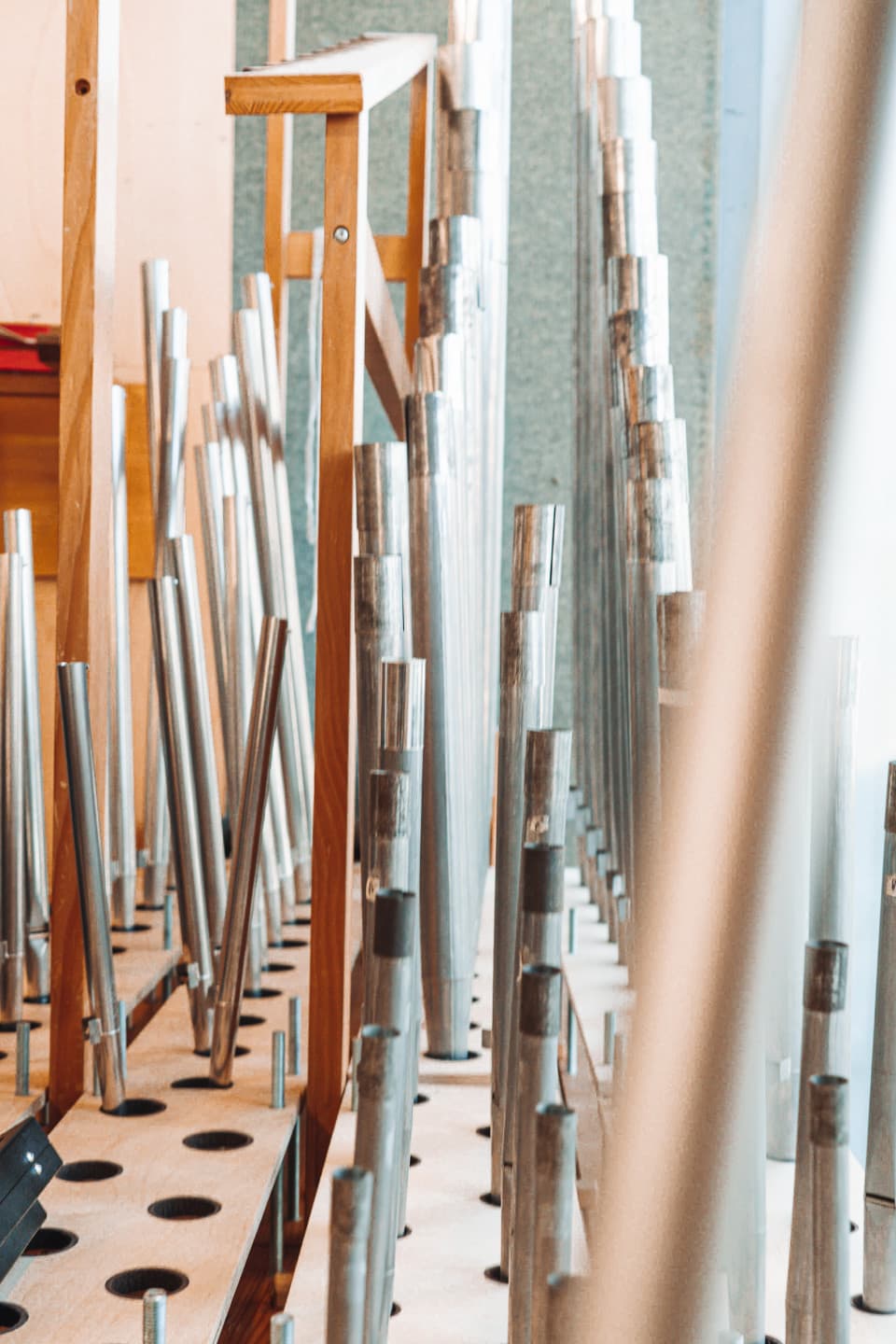
Entwicklungen von Rieger setzen den Standard im Orgelbau weltweit.
Rieger Electronic Assistant (REA)
Mit dem integrativen Setzer- und Steuerungssystem Rieger Electronic Assistant (REA) haben wir ein eigenes elektronisches System entwickelt, das sich durch seine hohe Funktionalität und Anwendungsfreundlichkeit auszeichnet. Im Vergleich zu handelsüblichen Speichersystemen erfüllt es die wachsenden Bedürfnisse von Organist:innen.
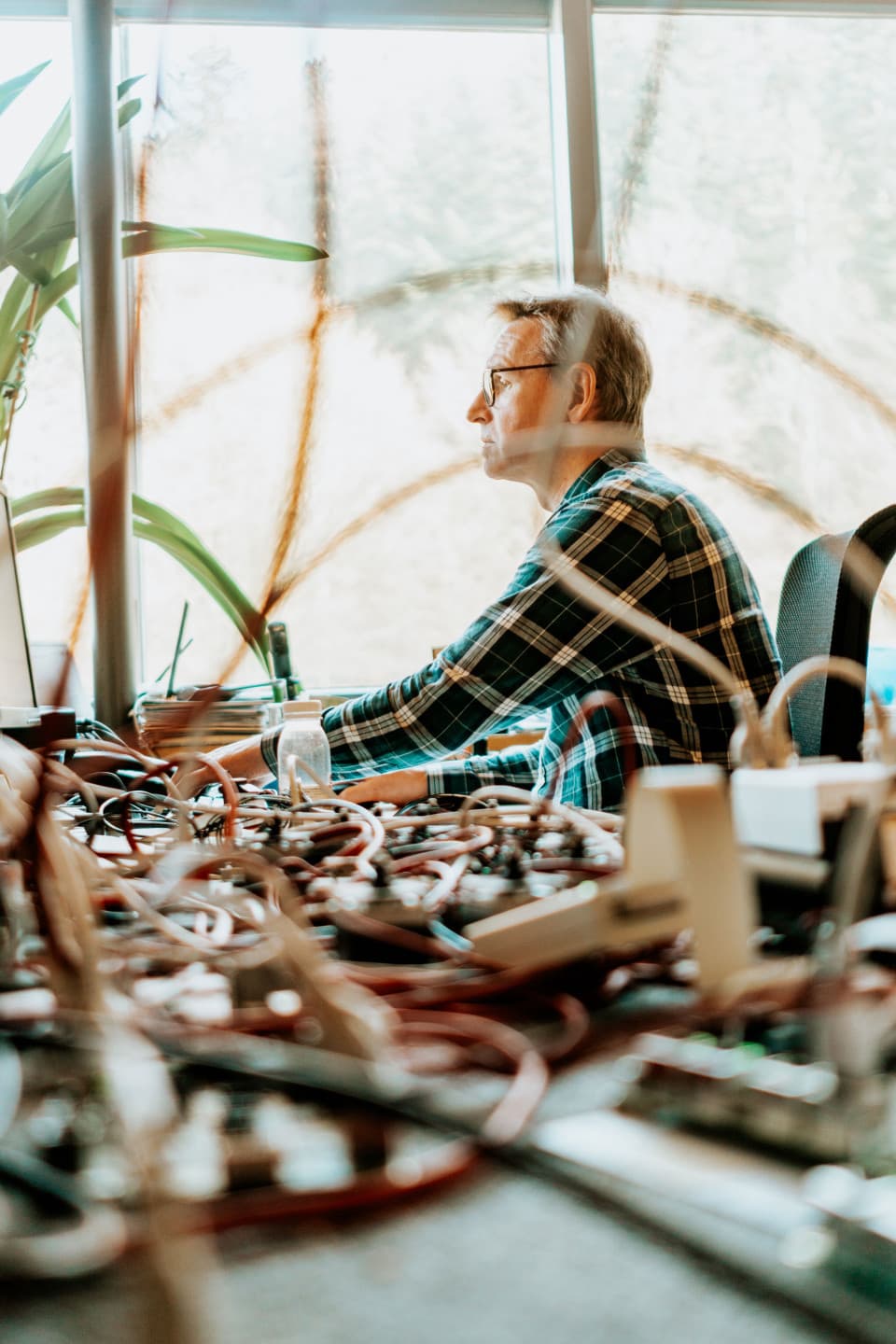
LEHRE ALS ORGELBAUER:IN
Kaum ein Handwerk ist so vielseitig wie der Orgelbau. In einem Beruf kommen verschiedene Gewerke zusammen: Von Holz- und Metallverarbeitung über kaufmännische Aspekte bis zu den sehr wichtigen künstlerischen Arbeiten. Schnuppertage oder Praktika führen zukünftige Lehrlinge in die vielseitige Welt von Rieger.
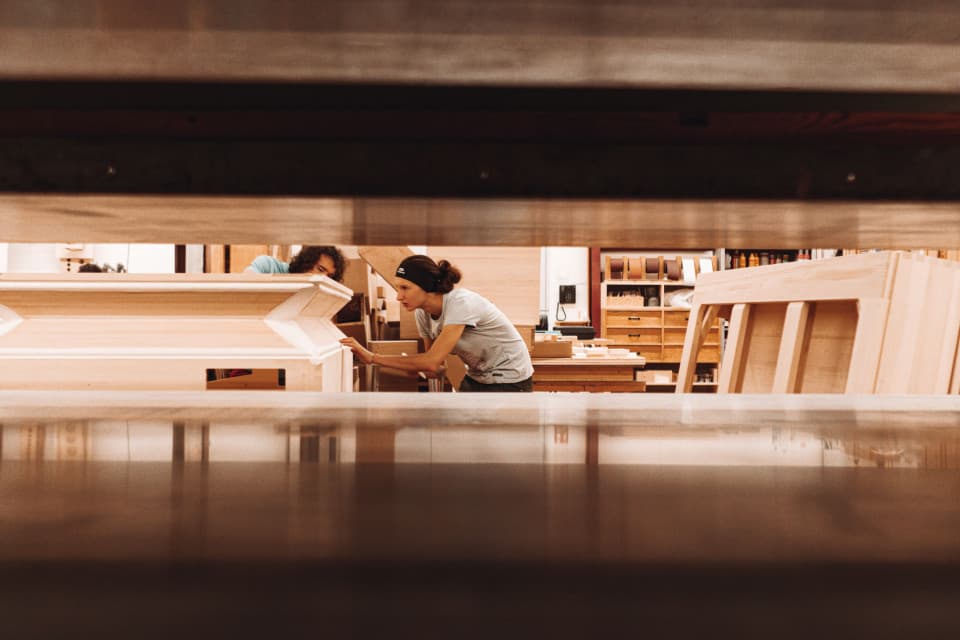
Wer in der wirklichen Welt arbeiten kann und in der idealen leben, der hat das Höchste erreicht.
Ludwig Börne